EProp Testing Comparison October 2020
Well, the EProp sure is different, with it’s very slender blades and all carbon fiber construction, including the hub. Weighs nearly nothing. Feels delicate but I guess that carbon fiber can do it if the builders know the material. Right away notice that it starts and stops without the jolts of heavier props; that’s really sweet! And runs very smoothly. It comes with a nifty digital protractor for setting the pitch.
Contrast the difference in width of those blades! The EProp has the narrowest blades I have ever seen on a power prop. My Kool would have one of the widest blades around. The thickness is also in the same ratio but I couldn’t get a good photo of that. This is sure going to be an interesting comparison test!
The instructions with the EProp mostly stress to set the WOT (wide open throttle) to 5500 rpm, but a special note recommends to set for 5800rpm for the Savannah. That’s the setting that I found to be the best for the EProp on my Savannah, as detailed later.
Testing at WOT 5500 rpm
But first I set it for 5500 which I found to require a pitch angle of 24.6 degrees.
First of all tested the EProp and a Bolly head-to-head both set to 5500 rpm WOT.
|
EProp 69” |
EProp 69” |
Bolly 66” |
Bolly 66” |
|
MAP |
RPM |
Speed |
RPM |
Speed |
Fuel burn (approx.) |
WOT |
5500 |
98 |
5500 |
98 |
26 |
26” |
5200 |
89 |
5180 |
90 |
20 |
25” |
4880 |
84 |
4910 |
85 |
17 |
24” |
4580 |
78 |
4580 |
78 |
14 |
23” |
4400 |
75 |
4420 |
74 |
12 |
Climb |
5250 2000-3000 ft |
950 fpm |
5000 2000-3000 ft |
860 fpm |
|
This demonstrates that both props performed exactly the same in speed when the engine power was exactly the same for each. The Bolly was way down in climb, just as the 66” Bolly that I tested years ago performed well in cruise but lagged in climb. (The 68” Bolly also tested back then climbed as well as any other prop, so diameter is important for climb.)
The lesson here is that if you re-pitch your prop to 5500 WOT then it will probably perform just as well as the EProp at that same setting, but I don’t recommend that you pitch any prop on a 912uls to 5500 WOT (more on that later).
But I really do like the EProp when pitched to 5800 WOT, as the data will show.
Testing at WOT 5800 rpm
The instructions with the EProp insisted on setting WOT to 5500 rpm, except when it later stated that for a Savannah that should be set to 5800 rpm…..
So I set it to 5800, which turned out to be a pitch angle of 22.6 degrees.
Then tested the EProp and a Kool head-to-head both set to 5800 rpm WOT.
|
EProp 69” |
EProp 69” |
Kool 69” |
Kool 69” |
|
MAP |
RPM |
Speed |
RPM |
Speed |
Fuel burn (approx.) |
WOT |
5800 |
98 |
5900 |
97 |
26 |
26” |
5540 |
92 |
5640 |
91 |
20 |
25” |
5250 |
86 |
5250 |
85 |
17 |
24” |
4930 |
79 |
4980 |
78 |
14 |
23” |
4710 |
75 |
4740 |
73 |
12 |
Climb |
5520 |
1000 fpm |
5200 |
1000 fpm |
|
This demonstrates that both props performed almost the same, difficult to measure the difference. With any single measurement I ignore one knot differences as being within the margin of error. However when I have done multiple tests with consistent repeatable results I think the margin of error can be taken as less than one knot. These results are from multiple tests in good conditions head to head and were very consistent. So, from these results I think I can conclude that the consistent one knot faster speeds with the EProp indicate the greater efficiency of that prop. That would be expected with the thin narrow blades of the EProp compared to the wide thick blades of the Kool.
But it is really remarkable that the performance is so similar despite the vast difference in form. Very much like the surprising results of those earlier tests at https://www.stolspeed.com/nid/46
I really liked the EProp when set at 5800 WOT.
Analysis:
When I did that earlier prop comparison testing, I started the analysis with this comment:
Engine power is RPM x Torque, so any testing that only compares at RPM settings isn't testing at the same power output. ie- If the prop is pitched for 5500 WOT rather than 5800, then cruising at 5000 will show a higher speed, but of course that's at a much higher percentage of total power than if WOT was 5800.
That’s exactly what’s happening here. If the EProp is pitched to 5500 rpm rather than the Rotax specified 5800, then flown at the same RPM as a prop that had been pitched to 5800, then of course it will fly faster because the engine is producing more power, maybe 85% instead of 75%. It’s not the new prop itself that’s giving the higher speed, it’s the increased power applied.
For instance, normal cruise at 5200rpm burns 3 litres/hr more fuel when pitched at 5500 rather than 5800, for an increase in speed of 5 kts.
Using Rotax’s Specific Fuel Consumption figure of 0.276L/hr/hp, that 3L/hr figures to about 11hp, which is considerable. Actually it’s getting close to Maximum Continuous Power specified by Rotax. That 5500 RPM for max continuous specified by Rotax is only valid if the WOT is pitched at 5800. So if 5500 is 300rpm down from 5800, then 300rpm down from WOT at 5500 is 5200 for max continuous. (I realize that it’s not necessarily linear, but close to it.) This is confirmed by the test data that shows that if the EProp is pitched to 5800, 26” MAP gives 5500rpm which is max continuous specified by Rotax, but if the prop is pitched to 5500 WOT then that same power setting of 26” MAP gives 5200rpm. So if you pitch your prop, any prop, to 5500 WOT, and cruise at 5200 you are at max continuous and flying about 5kts faster. If you fly any 5800 prop at max continuous of 5500 it will also fly at least 5kts faster than usual cruise.
A max continuous recommendation is determined by internal heat dispersion factors, not the actual RPM. Components such as exhaust valves and pistons need to transfer heat to the outside cooling system through valve guides and piston rings, and at continuous high power they can overheat due to the limits of that heat dispersion rate.
I realize this confusing, but I don’t know how to explain it better. It’s comfortable for me because I was testing engines for power and torque and specific fuel consumption in engineering school in the ‘59…..
MAP and actual engine power
Manifold Absolute Pressure (MAP) is an excellent measurement to determine actual engine power produced. It’s an easy instrument to fit and is accurate. Fuel burn is also an excellent measurement of actual engine power produced, but I don’t have a fuel flow gauge that has the precision to be definitive, but is still a good general indicator.
MAP doesn’t indicate actual engine output, but is very repeatable to set the same actual power output for each run, and thus good for comparison testing. I fly each comparison test at 2000 QNH in stable atmospheric conditions as similar as possible to the previous run. Then I fly a 4-way GPS orbit at constant power and altitude for every speed figure. Nearly get dizzy going round and round. Many test runs over the years have produced very repeatable consistent results with this method.
I find it very difficult to explain to flyers that the same engine RPM is NOT always the same power output. RPM is only half the formula; the other half is Torque.
Rotax specifies that for an engine pitched to 5800 WOT, the max continuous is 5500rpm.
That 5800 figure specified by Rotax is based on their assessment that it will run the engine in the most favourable rpm range for normal operation.
Testing showed that max continuous of 5500 when pitched to 5800 WOT equated to a power setting of 26” MAP at 2000ft.
However, with a prop pitched to 5500 WOT, 26” MAP gave 5200rpm.
Power = RPM x Torque, so at 26” for example, a reduction of RPM from 5500 to 5200 has increased the torque by about 11%.
Then the question is, do you want to run your engine
- at higher RPM and lower Torque
- or lower RPM and higher Torque??
Taken too far, the lower RPM and higher Torque becomes ‘lugging’ the engine…..
25” @2000ft is my usual cruise power, and with the prop pitched to 5800, that gives an airspeed of 85kts at 5200rpm. But if the prop was pitched to 5500 WOT then the RPM would be 4880 which I consider slower than best RPM, and somewhere I believe I saw a caution from Rotax that it was inadvisable to cruise in the 4800rpm range. (Can’t find that caution now)
And cruising at 5200 with the prop pitched to 5500 puts the MAP at 26”, which I have already indicated is near maximum continuous power…..
I don’t feel comfortable at either of those situations so wouldn’t ever pitch to 5500.
Probably doesn’t hurt the durable Rotax 912uls, but I heed Rotax specifications for this very expensive engine.
There are many aircraft flying with props pitched to 5500 – 5600 rpm for many years, so I guess it can be done. But if you want to run a prop set to 5500 WOT on a 912uls then I reckon you should contact Rotax for their advise. Not any third party…..
5800 WOT is excellent in all regards, and that is where I would pitch the EProp.
Small wonder Rotax stipulates WOT 5800.
Now here’s an interesting result!
Comparing the speeds produced by the EProp
when pitched at 5800 as compared to 5500,
each for the same amount of power produced by the engine as measured by the MAP.
|
EProp 5800 |
EProp 5500 |
Fuel burn L/hr |
|
|
|
|
26” |
92 @ 5540 |
89 @5200 |
20 |
25” |
86 @5250 |
84 @4880 |
17 |
24” |
79 @4930 |
78 @4580 |
14 |
23” |
75 @4710 |
75 @4400 |
12 |
Note that the EProp when pitched to 5800,
actually cruised FASTER than when pitched to 5500,
for the same power applied and same fuel consumption.
Many won’t believe that, but these are the results of careful testing.
I did these tests with all care and attention, and based on lots of experience in such projects.
No doubt many will disagree with some opinions, and I respect their right to disagree.
But facts are facts, and I must present the results that the test data produced.
- John Gilpin
Further thoughts……
I don’t quite understand the drive to fly a Savannah faster than the 80-85 kts range….
That is the design speed of the aircraft, and at those speeds the aircraft is very smooth, stable and easy to trim hands off for hours at a time.
When flying those tests at 90kts, I found the aircraft to be less stable, didn’t retain trim as well as before, some buffeting, and a feeling that it was being pushed harder than it wanted to go…..
Maybe the S model handles 90kts better, but it feels to me that the VG model doesn’t really like to go that fast…..
Just for interest, an increase in cruising speed from 85 to 90 kts
makes for a time saving of only 3.5 minutes per one hour travelled…..
............................................................................................................................................................................
Even more props comparison testing…..
‘Stump-pulling’ this time
Previous prop testing had surprisingly shown that all props have very much the same efficiency, with no measurable difference for cruise speed and climb when pitched to the same actual engine power setting. Earlier test results below explain that fact.
The real difference that I was wanting to test this time was the static pull. Previous testing had found that static pull gives no indication of cruise or climb performance. But of course it does make a difference in short takeoff performance. That initial thrust makes a big difference in how quickly the aircraft gets rolling and up to flying speed. With the popularity these days of seeking impressive STOL performance that could be significant.
So I purchased a digital load cell and set up a ‘stump pull’ arrangement to give all props equal conditions. I tested and re-tested to ensure consistent results. The differences in ‘grunt’ are significant.
Of course such results are also effected by atmospheric conditions such as Density Altitude. So I tested and re-tested to compensate for different conditions and selected an average that gave the most fair comparison.
This time testing a couple of new props from Meglin, being imported from the Ukraine by https://www.bushaero.com.au
Meglin used to be named Luga before some reorganizations over there. It seems there are three factories over there, which work together and compete.
The Kool prop that I’ve used for 11 years was also made in one of those factories, using the same techniques and materials and profiles, and all fit the same hubs. Kool was the name that a distributer in Canada re-branded the prop that I bought. I love that prop and now have 1100 hrs on it and it still looks like new, despite many ‘adventures’ operating off dirt strips and off-field landings outback. It’s mowed some tall grass and shrubs and kicked up sand and dirt but the stainless steel leading edge just gets more polished. All those props are very strong and smooth-running. They have thick sections and high-lift profiles which makes them completely rigid and stable. That stainless leading edge is very superior, being very strong and well-bonded with through rivets. The gelcoat is excellent quality and keeps its good appearance for many years. The butts of the blades are 50mm in diameter compared to the smaller butts on other popular props. All in all, they are very sturdy props.
The Meglin factory is the only one that manufactures the scimitar-shaped blades. They also make a wide range of props for different uses as shown in the website.
https://www.bushaero.com.au/composite-propellers
The three models that I tested are:
The scimitar-shaped SR-107 3-blade 72”,
The scimitar-shaped SR-106 3-blade 70”
and the scimitar-shaped SR-107 2-blade 72”.
My 69” straight-blade Kool would be the same as the CR-104 listed.
I included the Kool in the testing as a reference, having been through many tests over the years.
Spinners are available for these props but I didn’t want them in the way for all the bolting/unbolting of prop changing and re-adjusting.
(Besides, I figure spinners on STOL aircraft are like hub caps on a 4WD…)
To do this thrust testing I purchased an electronic load cell and tied it off to a stump as below. Then placed the wheels on boards on level ground to eliminate rolling resistance in the grass.
Meglin 3-blade 70”
Meglin 2-blade 72”
Static Thrust Testing Results
Prop / Diameter | WOT rpm | Static rpm | Thrust kg |
Meglin 3-blade 72" | 5800 | 4900 | 196 |
Meglin 3-blade 70" | 5800 | 5200 | 195 |
Meglin 2-blade 72" | 5800 | 5220 | 190 |
Kool 69" | 5800 | 5050 | 190 |
Bolly 68" (Average 5 props) | 5800 | 5200-5300 | 165 |
Kiev | 5800 | 5230 | 165 |
EProp | 5750 | 5750 | 155 |
So there is a considerable difference in static thrust, and this was noticeable when flight testing, in that the Meglin props had more immediate ‘grunt’ when the throttle was opened and takeoff roll was reduced.
30 kg thrust makes a big difference.
It’s not really practical to measure actual takeoff roll at this airstrip due to changing grass length, strip not level, and varying wind conditions, but a Savannah owner who tried the 72” 3-blade from his very short strip with tall trees at the end, noticed a considerable improvement compared to his Bolly.
Notable here is how the EProp produced the lowest static thrust, and the engine revved out to the same as it’s WOT! So it didn’t have nearly enough blade area to couple with the air at that full power setting at no airspeed, and there was heaps of slippage and cavitating. This backs up the observation by an experienced instructor who tried the EProp and noted that when he applied full power in a low speed go-around he got lots of revs but little immediate thrust…. Also noted by an observer off to the side, was that the blades flexed (coned) considerably forward under power. I guess the manufacturer knows what they’re doing, but I sure don’t like the idea of all that flexing going on in such a high revving highly loaded critical component...
Cruise performance
These are the results of the recent testing.
72" 3-blade | 72" 2-blade | 70" 3-blade | 69" Kool | |
WOT rpm | 5800 | 5800 | 5800 | 5800 |
Static pull kg |
196 |
190 | 195 | 190 |
@ rpm | 4900 | 5220 | 5200 | 5220 |
Climb 2000-3000ft fpm |
910 | 1034 | 1000 | 980 |
@ rpm | 5120 | 5320 | 5300 | 5200 |
Speed tests | ||||
MAP @ 2000 ft | Kts @ rpm | Kts @ rpm | Kts @ rpm | Kts @ rpm |
26" | 92 | 92 | 92 | 92 |
5650 | 5660 | 5520 | 5610 | |
25" | 86 | 87 | 85 | 85 |
5300 | 5430 | 5250 | 5160 | |
24" | 77 | 80 | 78 | 79 |
4800 | 4970 | 4850 | 4910 | |
23" | 73 | 75 | 75 | 74 |
4700 | 4800 | 4650 | 4660 | |
5000 rpm | 79 | 81 | 81 | 80 |
Interpolating those results to correlate to rpm, which more flyers are used to:
(All props pitched to WOT of 5800 rpm) Results from earlier testing.
RPM |
Meglin 72” 3-blade |
Meglin 70” 3-blade |
Meglin 72” 2-blade |
Kool 69” |
|
Bolly 68” |
Kiev 71” |
EProp 69” |
5500 |
89 |
91 |
90 |
89 |
|
91 |
91 |
91 |
5200 |
84 |
84 |
83.5 |
84 |
|
85 |
86 |
85 |
5000 |
79 |
81 |
80.5 |
80 |
|
79 |
81 |
81 |
Previous tests of the Bolly and Kiev gave speeds 1-2 kts higher, but those tests were done in winter with cool dense air.
These results reflect more equal conditions.
I know that this consistency is hard to believe, but it’s proven many times over by careful testing.
I’m constantly amazed to see the end results so consistent when averaged over multiple tests.
Not more than 2kts difference between all props!
I would expect that the variation would be greater, considering different prop shapes, atmospheric conditions and measurement variations, but not so.
It’s easy enough to err with instantaneous readings, either by accident or wishful thinking, but averaging multiple tests over time weeds out the variations. Also temperature and density altitude make a difference, as we notice on some days when the aircraft just goes a lot better. These results are averaged from countless tests in varying conditions. All tests done very early morning in steady conditions at 2000QNH about 20°C, over water to minimize thermal activity.
4-way GPS runs are really excellent in that regard. There’s almost always some breeze up there, so the ground speeds for different legs vary by 10 kts or more, but when summed and divided by four the results are remarkably consistent, over and over again. Of course, at the completion of the 4-leg orbit the altitude must still be the same as starting, and that’s an excellent control on flying precision. It’s all too easy when taking instantaneous one-way readings to inadvertently take the indicated speed reading when climbing or descending slightly (seems to happen more often when descending when the ASI reads higher…) a descent rate of only 50fpm makes a considerable difference.
I reckon everyone needs to do some 4-way GPS runs to determine really what speed they’re making through the air. Also an opportunity to calibrate your ASI. Instantaneous GPS comparisons or even two-way GPS runs are useless. I’ve now done what seems like hundreds of such 4-way orbits, in varying conditions, and continue to be amazed that the averaged result is so consistent.
Climb
Also need to do proper climb rate tests. I keep hearing of claims of 1500fpm etc, but I have never measured much above and usually around 1000fpm for a sustained climb behind a 100hp Rotax pitched to 5800 WOT. Once again instantaneous readings are open to big errors due to zoom climb and wishful thinking. I never depend on a VSI, but climb at exactly 60kts for 1000ft timed by stopwatch. I use between 2000 and 3000ft to not annoy residents on the ground and realize that the rate will be a bit less at that altitude than at sea level, but then we don’t usually fly at sea level….
Conclusions
These results indicate that the Meglin range of props showed considerably greater static thrust than all others tested, but still showed the same cruise speeds as all other props. Which makes them well suited for all aircraft, but especially well suited for owners seeking shorter takeoff performance.
The Meglin 70” 3-blade gave the best overall results on a Rotax 100hp.
p.s.-
I realize that the consistency of these results make it look like they've been 'cooked'.
If I saw such results for the first time I would be skeptical as well.
But I guarantee that isn't the case.
If anyone else wants to do similar tests then please do so.
But they must be done using the same parameters and care and attention to repeatable detail.
............................................................................................................................................................................
Older Prop Test Comparisons
From top to bottom
66" Bolly
68" Bolly
69" Kool
69" Aon
71" Kiev
(The spots on the blades are for measuring pitch at 600mm from centres)
For these tests, the props were pitched to give 5200 rpm at best climb rate of 57 kts.
Rotax specifies that rpm at climb should not be less than 5200.
This pitch gives 5900 at wide open throttle (WOT) straight and level with two props.
This is 100 rpm above the red line, but to pitch for 5800 WOT will give a climb at less than 5200.
We never run WOT straight and level anyhow, but we do climb every time we fly, so I'll set for 5200.
The test flights using manifold pressure as the reference, gave incredibly equal results for all props – all within one knot of each other! One knot is less than the tolerance of the measuring ability.
So effectively, each prop gave exactly the same speed for the same power setting!
Engine power is RPM x Torque, so any testing that only compares at RPM settings isn't testing at the same power output. ie- If the prop is pitched for 5500 WOT rather than 5800, then cruising at 5000 will show a higher speed, but of course that's at a much higher percentage of total power than if WOT was 5800. Ideally we should test at equal fuel flow rates, because that truely indicates engine power, but that's difficult to determine accurately in real time. I've tried fuel flow meters, and don't find them accurate enough, at these flow rates, to be useful for good test comparison. The only way I've found to get truely accurate fuel flow measurement is to measure the fuel used on a three hour flight at a constant power setting, which gets a bit time consuming for multiple tests.
As I understand it, manifold pressure is quite a good indicator of actual engine power output, provided altitude and air density are equal. So I've done the cruise speed comparisons at equal manifold pressures, all at 2000' QNH, and all at very similar atmospheric conditions.
Flight Test Results
|
Kool 69" |
Kiev 71" |
Bolly 68" |
Bolly 66" |
AonProp 69" |
---|---|---|---|---|---|
WOT (rpm) |
5900 |
5900 |
5810 |
5800 |
5800 |
Pitch |
16.5 |
16.25 |
19 |
20 |
15 |
Time to Climb |
60 |
60 |
60 |
76 |
60 |
RPM |
5170 |
5170 |
5200 |
5240 |
5230 |
|
|
|
|
|
|
Static RPM |
4930 |
5070 |
5230 |
??? |
5240 |
MAP @ 2000ft |
kts / rpm |
kts / rpm |
kts / rpm |
kts / rpm |
kts / rpm |
26" |
92 @5610 |
92 @5490 |
93 @5500 |
92 @5500 |
93 @5500 |
25" |
85 @5160 |
86 @5160 |
85 @5030 |
85 @5230 |
86 @5200 |
24" |
79 @4910 |
80 @4840 |
79 @4800 |
79 @4850 |
79 @4800 |
23" |
74 @4660 |
75 @4640 |
??? |
75 @4630 |
75 @4500 |
|
|
|
|
|
|
It's interesting to have a look at the differences in profile and helix between different props,
but the performance is very much equal.
AonProp Kiev Kool
Analysis
Just as in the earlier prop tests, I could find no real difference in cruise speed between any of the props tested, when equal power was carefully applied to each.
So it would seem that when someone claims a big difference with a different prop, they are probably depending solely upon RPM, and are actually applying more less power.
The only difference found was that the smaller diameter Bolly was considerably degraded in climb.
This has been confirmed by two real life cases that I know of, who changed from the 66" Bolly to the 70", and both reported considerably better take-off and climb performance.
Kool
![]() |
![]() |
![]() |
It runs as smooth, and stops with much less jolt than the Warp. Ground observers noted that the noise produced at cruise and full power at 800ft AGL was considerably less than the Warp. Kool also produces a version with anti-vortex tips to reduce noise even further. I know of a Savannah that has that prop, and we’ll do a noise comparison when we can get together.
The hub is fairly plain, with a matt black finish. It uses the standard 75mm bolt pattern.
For 5200rpm in climb, the pitch at 600mm from the centre measured 16.5º.
I've decided that this is my favorite prop.
Very strong and smooth running. Very good L/E protection.
I have about 400 hrs on it now, mostly on grass and dirt strips, and it's still looking good.
Vasili at http://www.airtrikes.net/propellers.shtml in Canada seems to be the main distributor for America, but several customers I know of have had long delays to get supplied....
http://www.lugaprop.kiev.ua/catalog_en.html has been mentioned on this forum before, with good service. To order again I would go direct to this Ukrainian supplier. Looking at his catalog I reckon the R104/L104 to be the same as the 69" Kool that I tested and still love.
![]() |
![]() |
The Bolly props are an Australian design and well-known here as a high quality prop. They tried having them made in China, but weren't satisfied with the quality, so are now manufacturing in Australia again. They're now under new ownership with big plans to become a world prop manufacturer.
Hans started with a Woodcomp on his 701, but it snapped off cleanly at the junction to the hub when it nicked the ground while taxiing through a dip..... (The butt of the blade was seen to be hollow!). He used his first Bolly for about 600hrs and loved it, until dropping the nose wheel into a rabbit hole destroyed it..... He immediately replaced it with a new Bolly.
The Bolly blades are considerably lighter than the Warp Drive blades, so the rotational inertia is noticeably less. This makes it smoother running, and considerably less jolt on start and stop. The blades are wider than the Warp and a more rounded shape as seen in the photos. The 'Duratuf' leading edge protection is a heat-cured polyurethane, moulded into the leading edge. It’s resilient and very effective protection against chipping. The Bolly hub also uses the 101.6mm bolt pattern and drive lug system, particularly suitable for the 100hp engine. It's very nicely machined, solid, and attractive so it doesn't really need a spinner.
The labeling of this BOS range of Bolly props is a bit strange.....
The so-called 70" prop is really 68", and the so-called 68" is really 66"???
This because they changed the design of the hub and kept the designations the same.
The Bolly blades do fit in a Warp Drive hub, and when using that hub then the actual diameter is the 70" and 68" as labelled. Is that clear now??
So I've used the actual diameter when referring to them in the test results.
The tips of the Bolly aren’t flat, so can’t measure pitch at the tip. So I used the standard 600mm (2ft) out from the centre, where it measured 19º for 5800rpm WOT..
Kiev
I don't have photos of the Kiev, but it's a slim, elegant prop.
Very efficient, and smooth running. Considered to be a standard as among the most efficient.
A friend has one for 400 hrs on these dirt strips, and it's showing it's wear more than the the Bolly or Kool.
The brass leading edge is considerably dented and tarnished, but still performing well.
There can be a delay in getting one, as they can't seem to keep up to demand.
AonProp
light.avia@gmail.com
The AonProp company sent me this one for testing. It's made in the Ukraine, to much the same good standard as the Kiev and Kool.
One problem that I found is that the large helix in close to the base meant that I required a 20mm spacer to fit it on my Savannah so that it cleared the cowling.....
It gave the best static thrust, but as a wise guy once said, "....That's irrelevant because you don't fly tied up to a tree anyhow...." Well, quite right, static thrust doesn't really mean much even in take-off performance. I've found that it only affects the very initial part of the take-off roll, and as soon as the aircraft is rolling a few miles an hour any advantage in static thrust is nullified.....
.......................................................................................................................................................................
Even Earlier Prop Comparisons
This is from an earlier prop test comparison.
Manifold pressure readings aren't quite comparable due to a different gauge used,
but the results are the same, in that all props gave the same speed for the sme power.
Even props as completely different as the Peszke and the Brolga!

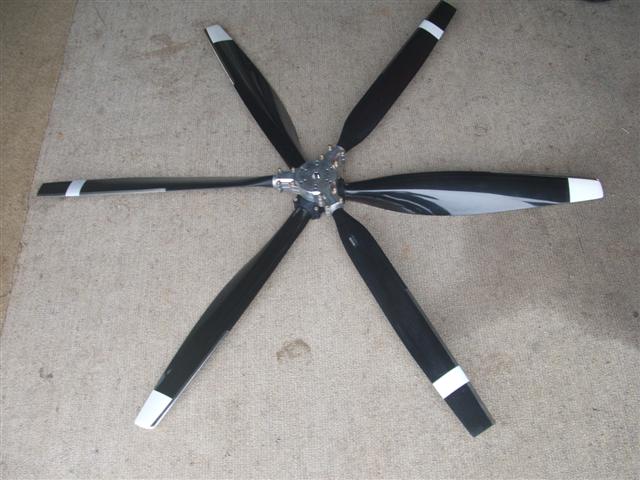
Pitch was measured with a Warp Drive protractor – a very good instrument, worth getting whatever prop you are using. It’s very easy to use and gets repeatable results right down to a quarter of a degree.
![]() |
![]() |
|
Warp Drive |
Bolly |
Peszke |
Kool |
Brolga |
|
70" |
70" |
68" |
70" |
68" 4-blade |
|
|
|
|
|
|
WOT (rpm) |
5800 |
5800 |
5800 |
5800 |
6000 |
Pitch at tip (degrees) |
12.5* |
*** |
?? |
11.25* |
16* at hub |
Pitch at 600mm from centre |
19.5* |
19* |
|
17.5* |
|
|
|
|
|
|
|
@ 5000rpm (knots) |
81 |
82 |
81 |
82 |
78 |
|
|
|
|
|
|
Climb 2000'-3000' (sec) |
60 |
60 |
60 |
|
60 |
RPM @ 55 kts climb |
5180 |
5100 |
5350 |
|
5100 |
|
|
|
|
|
|
Static Thrust (kg) |
194 |
196 |
184 |
196 |
186 |
Static RPM |
5020 |
5000 |
5400 |
4920 |
4880 |
|
|
|
|
|
|
|
|
|
|
|
|
Manifold Pressure |
|
|
|
|
|
26" @ 2000' WOT |
5800 |
|
|
5800 |
6000 |
25" |
86 @ 5380 |
|
|
87 @ 5260 |
86 @ 5540 |
22.5" |
77 @ 4780 |
|
|
76 @ 4680 |
76 @ 4940 |
![]() |
![]() |
![]() |
![]() |
The Bolly props are an Australian design and well-known here as a high quality prop. They tried having them made in China, but weren't satisfied with the quality, so are now manufacturing in Australia again. They're now under new ownership with big plans to become a world prop manufacturer.
The tips of the Bolly aren’t flat, so can’t measure pitch at the tip. So I used the standard 600mm (2ft) out from the centre, where it measured 19º for 5800rpm WOT..
![]() |
![]() |
This prop is now on a Zenith 701 with 80hp, and performing really well.
|
The relatively flat blades give good performance at those speeds, and excellent take-off performance, but I expected that they would run out of puff at higher speeds compared to the high-helix props like the Bollie and the Kool. But testing shows this not to be the case, in that at the same manifold pressure settings, the Brolga performed at 86kts, within one knot of both the Warp and the Kool! The pitch blocks only come in one degree steps. 16º is a bit too fine for cruise, giving WOT 6000rpm, but 17º is over-pitched for best take-off. Since the Brolga is under-pitched, the rpm for the same manifold pressure setting is higher, but the speed was still the same...... I had expected that this large 4-blade prop would be best at take-off and noticeably slower at such speeds, but it seems not to be the case....... At WOT it gave 100+ knots, same as all the others, which was really surprising!
I’ve used this Brolga for 400hrs, and the only down-side is that, on long trips alongside a Kiev on another Savannah , the Brolga consumes one litre/hr more fuel, probably due to the extra drag of the 4-blade configuration, but I can’t measure a difference in testing. 4-blades is necessary with the Brolga because the three-blade cavitates some on take-off. Of course the 4-blades made for a smooth running and quiet prop, despite it’s rather ‘agricultural’ look.
I originally chose the Brolga because the factory is nearby, the price was right, and I have had good performance from them on earlier ultralights for 1200+hrs.
Unfortunately the Brolga is now out of production.......
Kool
![]() |
![]() |
![]() |
It runs as smooth, and stops with much less jolt than the Warp. Ground observers noted that the noise produced at cruise and full power at 800ft AGL was considerably less than the Warp. Kool also produces a version with anti-vortex tips to reduce noise even further. I know of a Savannah that has that prop, and we’ll do a noise comparison when we can get together.
The hub is fairly plain, with a matt black finish. It uses the standard 75mm bolt pattern.